The future of building construction sites after COVID-19. Could 3D Printing be the solution?

An aspect of the lock-downs and social-distancing precipitated by the COVID-19 pandemic is the complete overhaul of our business locations. Businesses that have adopted digital solutions seem to be making operational progress compared to those that still have not taken the innovative step towards digitalization.
In the construction industry; a deeply conservative industry, digitalization seems to be making some footprints in terms of the so-called Building Information Modelling (BIM). A tool which requires that construction projects are “built” twice; first digitally then in real terms. This approach rights reveals aspects of the entire construction project that needs to be optimized or de-risked. The BIM factors all construction processes as well as schedules drawing on the experiences of experts to decide wisely on work to be done. At the heart of this building approach is of course the population of human works on site. Most construction sites require the use of an “army” of workers closely interacting often time under physically demanding conditions. Social distancing is difficult to observe and wearing of masks simply isn’t healthy due to insufficient Oxygen supply needed to keep the energy tempo required on site.
Clearly should social distancing and the wearing of protective masks be essential for winning the fight against COVID-19 then that fight can not be won on a building construction site based on current habits.
3D-Construction Printing techniques fit quite well into a BIM concept though it significantly cuts-back on the amount of human presence at the construction site. Irrespective of the size of building being constructed 3D-Construction demands for the presence of a CAD engineer at the printer console, a materials specialist at the feeding controls, a structural engineer to inspect the built-up structure and an architect whom must not be constantly resident on site. The interplay between these site actors are digitally networked requiring that they work appreciably “social-distanced” with digitally equal access to the work progress at every aspect of the workflow.
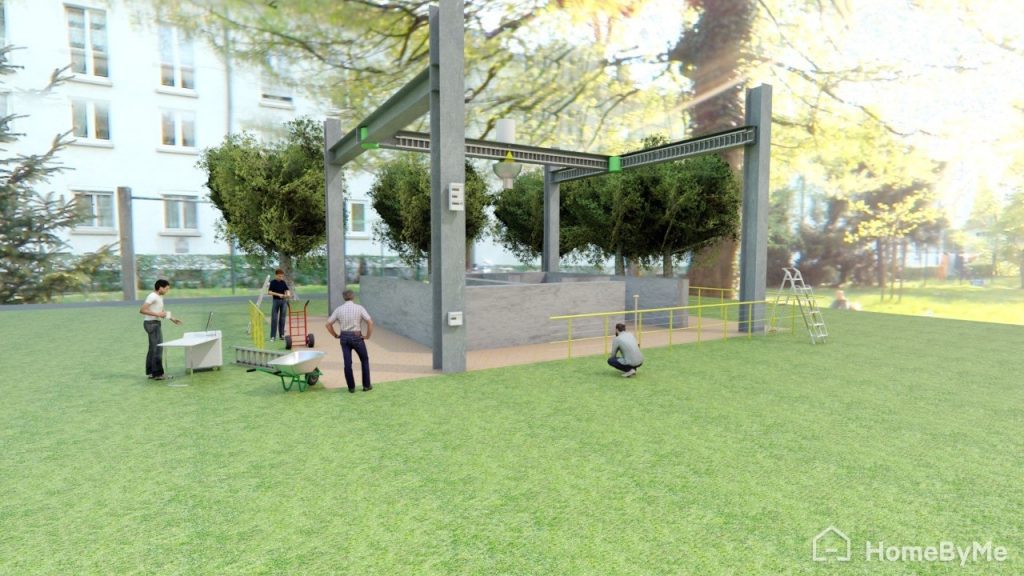
Post COVID-19, this is what the construction industry needs to be aiming to realize. Only 20% of the companies in the construction industry in Germany have a mature BIM strategy while about 40% are in the process of developing one. Whilst 10% of tenders in the construction industry are BIM conditioned more than 60% of experts implementing this strategy claim that it is technically challenging and time consuming. About half of the experts claim that high investments and lack of skilled labour are the key mitigating factors against BIM. It is considerate to state that the tools we use in 3D-Construction Printing is a compact BIM of some sort. It allows for building the house twice; a digital copy produced through simulation by software tools and then the actual copy produced by laying materials on site in the sequential fashion until the house is completed. At IMAPS, we offer the gateway to this building strategy. A strategy that allows you to optimally plan, execute and manage your building construction work onsite in record time.